BB Tools
BB APMT Carbide Insert CNC Machine Indexable Milling Tool APMT1604 APMT1135
BB APMT Carbide Insert CNC Machine Indexable Milling Tool APMT1604 APMT1135
Couldn't load pickup availability
Share
BB® Carbide Indexable Milling Inserts
Carbide-10pcs
PCD & CBN -2pcs
Label of shape and size
① AMPT 1135 08PDER
② AMPT 1604 08PDER


BL2060
Better hardness and wear resistance,
Machining reference:
P20,NK80,738,718,Mold Steel finishing machining
Stainless steel, steel, die steel, hard steel, superalloy and so on
rpm: 3400, feed:2400, ap=0.11mm
BB2055-FM
PVD coating TiAlN+CrAlN +TiSiN
Applicable to steel, stainless steel, cast iron, cast steel etc. HRC30~50.
Uniformly distributed sub-micron grade WC grains provide high hardness, while the reasonably controlled alloy composition enhances the solid solution strengthening of the binder phase, ensuring the high toughness of the matrix. The multi-layer composite coating features a TiAlN bottom layer that increases the bonding force with the matrix, an AlCrN functional layer with superior high-temperature performance, and a TiSiN surface layer that reduces the friction coefficient between the coating and the workpiece. The elastic modulus of the coating matches that of the matrix, resulting in a strong film-substrate adhesion.
*Cutting reference (Mold machining):
When we machining moulds, usually use these Insert to do rough machining and semi-finishing machining.
①APMT1135, for 16mm or 17mm diameter holder, RPM(S):2000, Feed:2500,ap:0.15~0.2, recommended 0.15 (increase the service life of Insert.)
②APMT1604, for 25,26 or 32mm diameter holder,
RPM(S):1600~1800,Feed:2500,ap:0.15~0.25
Parameters are also related to the extension length of the cutter.
PVD coating,AlTiN,
For General
The dedicated matrix material for mold milling cutters, with ultra-fine grains and a special ratio, enhances the wear resistance and toughness of the matrix, reducing the risk of edge chipping.H2&M2
M2- finishing machining. When in use, the transverse margin is less, and its angle is relatively sharp. If the margin is large, the angle will collapse easily. The finish for finishing is better than H2.
H2-rough machining , its angle is relatively blunt, so it doesn't matter if the margin is large, and it is not easy to collapse.
BF2055
Application: Aluminum, copper and other non-ferrous metal machining.

G2
G2 is mainly used for rough machining
MA
MA-Mainly used for finishing
*Note that MA is generally suitable for shell mill。
Not suitable for cylindrical milling bar.
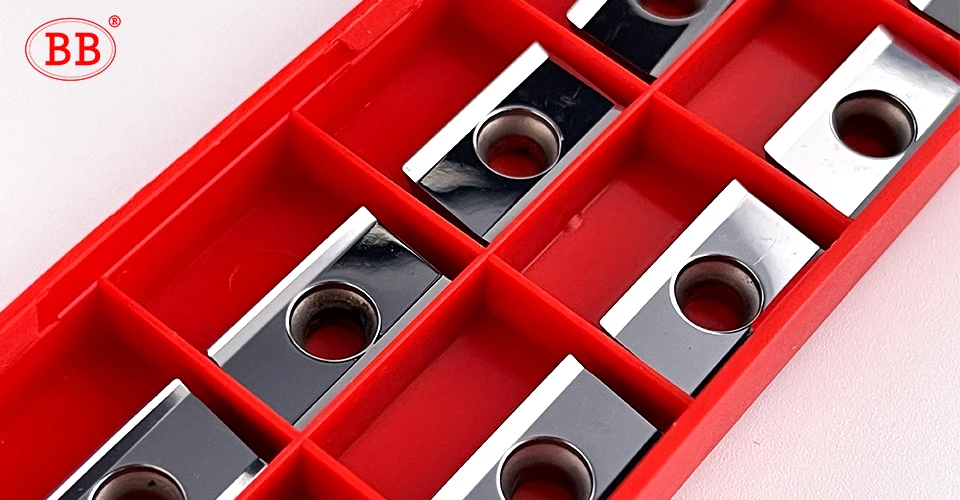

PCB&CBN
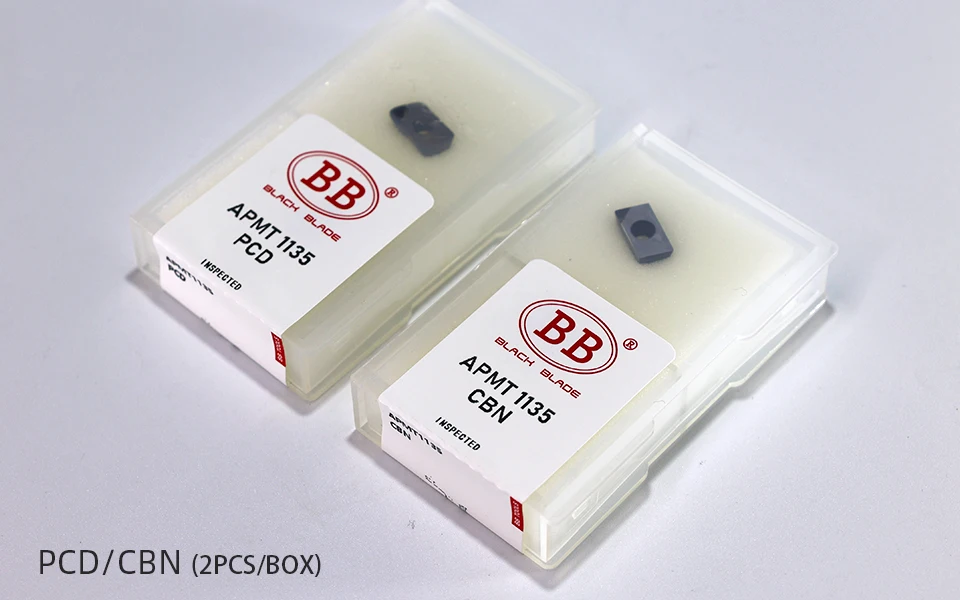
PCD:
for aluminum and aluminum alloys, copper and steel alloys, cemented carbide, titanium, magnesium, zinc, lead, etc.
Glass Fiber, carbon fiber reinforced plastics and other non-metallic.
N: Vc: 200~1000,F:0.05~0.5, ap:0.05~1
CBN:
for ferrous, it has extremely stable chemical properties. Capable of roughing and finishing turning hardened steel, bearing steel, high speed steel, tool steel, chilled cast iron, also competent for high-temperature alloy, thermal spraying materials, carbide containing more than 10% CO and other difficult-to-process materials of high-speed cutting. It can replace grinding by turning, and greatly improve the machining efficiency.
K:Vc=200~400,F=0.05~0.4, ap=0.1~1.5
S:Vc=50~150,F=0.05~0.3, ap=0.05~0.4
H:Vc=50~200, F=0.05~0.2, ap=0.05~0.2
HI, welcome to BB official store.
-We are professional manufacturer ,development and production of milling tools.
-We provide various tools for you . You can follow us and see more.
-You have free choice of collocation, pick different specifications and other tools in our store to you cart and pay them together. We will send the products you have picked as a package.
-Take an additional discount when you buy 10 pieces or more.
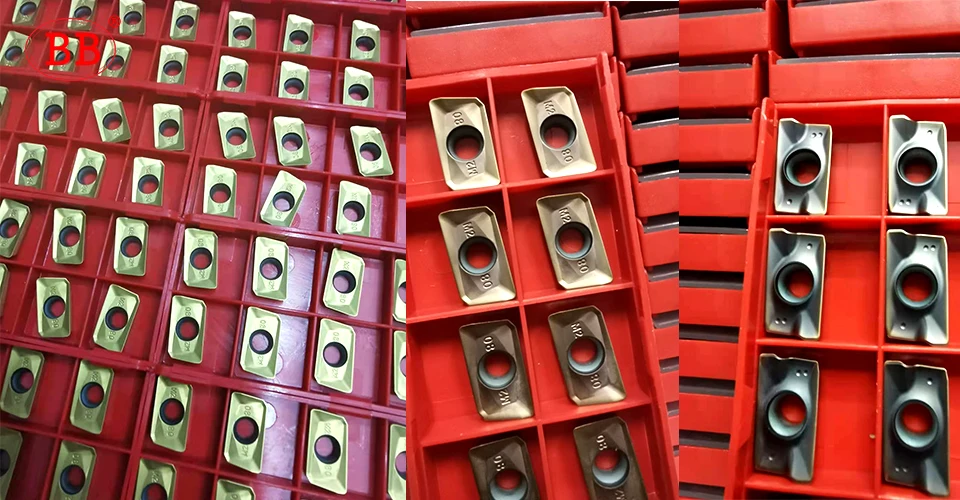
SHIPMENT
-We have already paid 80% of delivery cost .
-Orders processed timely after the payment verification.We ship products within 3 working days.
-The trade is cross-border, and Airmail is cheapest post which take a long time for delivery.If you need the item urgently ,please choose Express way.
-If you have not received your shipment within 60 days from payment, please contact us. We will track the shipment and get a reply to you as soon as possible.
We sincerely hope that BB tools will meet your full requirements. Please enjoy your online shopping.
How to improve machining efficiency and tool life
--Adequate cooling, proper processing linear speed, effective chip breaking and reasonable tool wrap angle are very effective for controlling the temperature of the tool tip.
For CNC machine tools and cutting tools with internal cooling at the same time, the internal cooling function that is most conducive to cooling should be used as far as possible, so as to make strong high-pressure water flow take away a large amount of cutting heat and ensure that the processing area is kept within a certain temperature range. Even for machining equipment without internal cooling function, it is recommended to use external internal cooling tool handle to enhance cooling pressure and improve cooling effect.
--Properly control the cutting force and cutting speed of the cutter
Generally, the hard-to-process materials are usually processed with fine grinding cutting edge, smaller cutting depth and cutting width. According to different factors such as difficult-to-process materials, parts structure and processing equipment, it is very important to choose a reasonable cutting line speed.
-Cycloid processing, spiral interpolation and large feed milling
The cycloid cutting method can minimize the cutting area to minimize the actual cutting wrap angle of the cutter and prolong the heat dissipation time of each tooth of the cutter; Spiral interpolation makes the cutting amount of each tooth relatively uniform, especially at the corner is the most obvious; The cutting method of large feeding effectively reduces the cutting force with small cutting depth and large feeding, making the minimum cutting heat generated in the machining and the lowest temperature in the machining area.
--Ensure processing interruption chips
Generally, in metal processing, a large amount of cutting heat is generated on the chips. Effective chip cutting will make a large amount of cutting heat generated in the processing be taken away by the chips. In general, we do not want long chips to be produced during processing. More attention should be paid to the processing of hard-to-process materials, especially for rough machining process, under the condition that the rigidity of the whole machining system allows, it should be made as broken as much as possible in the whole machining process, and reverse milling method should be adopted as much as possible to make the formed iron filings become thinner from thickness, and the shape of the iron filings is "9", "6" or "C.
--Effective Tool Wrap angle
The effective wrap angle of the cutter is reflected in the cutting parameters, which is directly related to the cutting depth Ap, the cutting width AE and the diameter Dc of the cutter. Especially when processing hard-to-process materials, full cutting should be avoided as much as possible. In actual processing, the tool life will be reduced by about 30% every time the cutting wrap angle of the tool doubles.
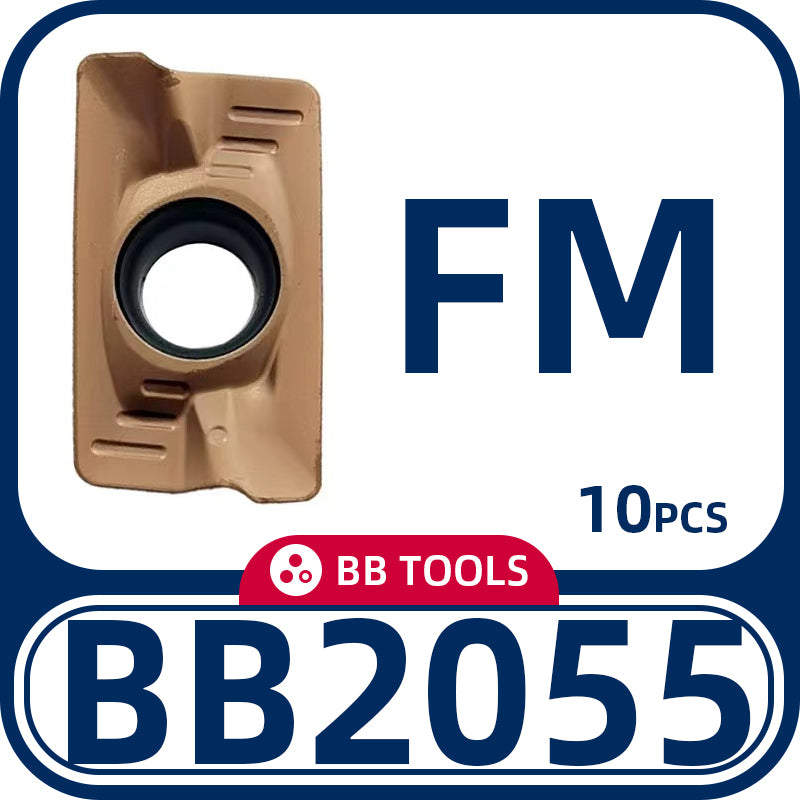
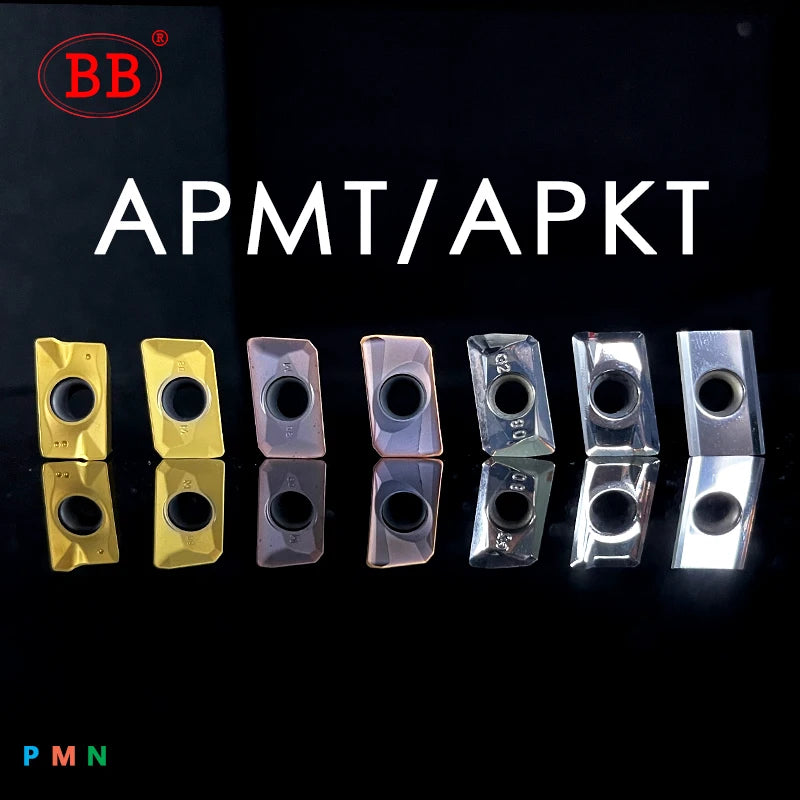
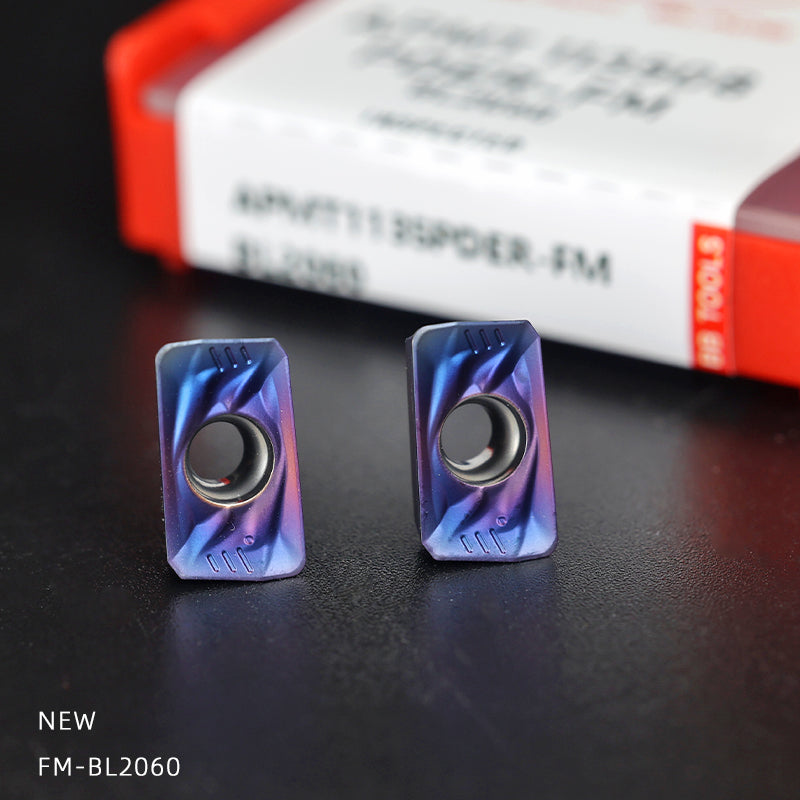
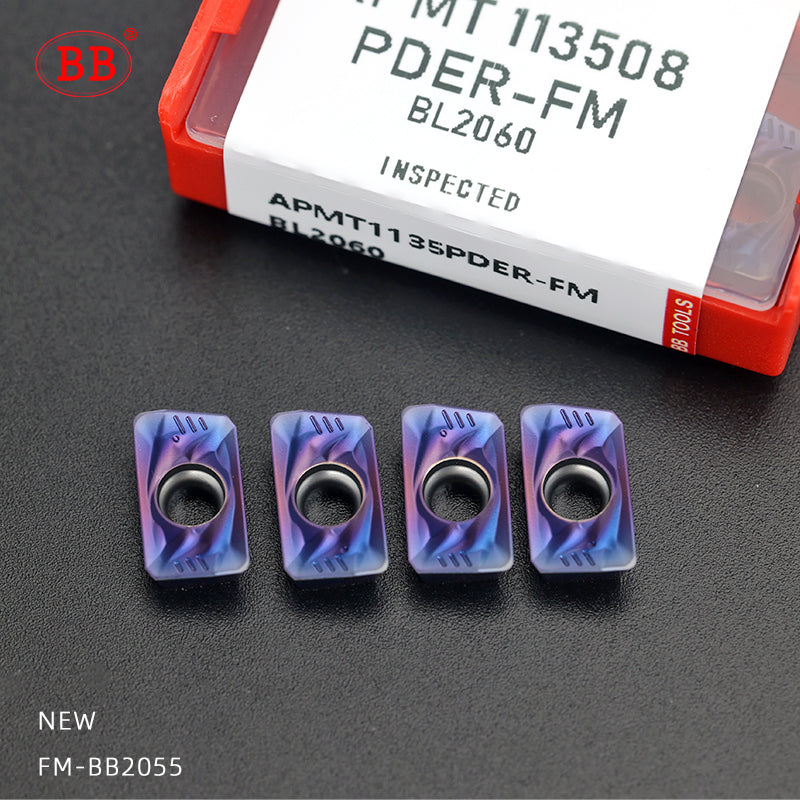
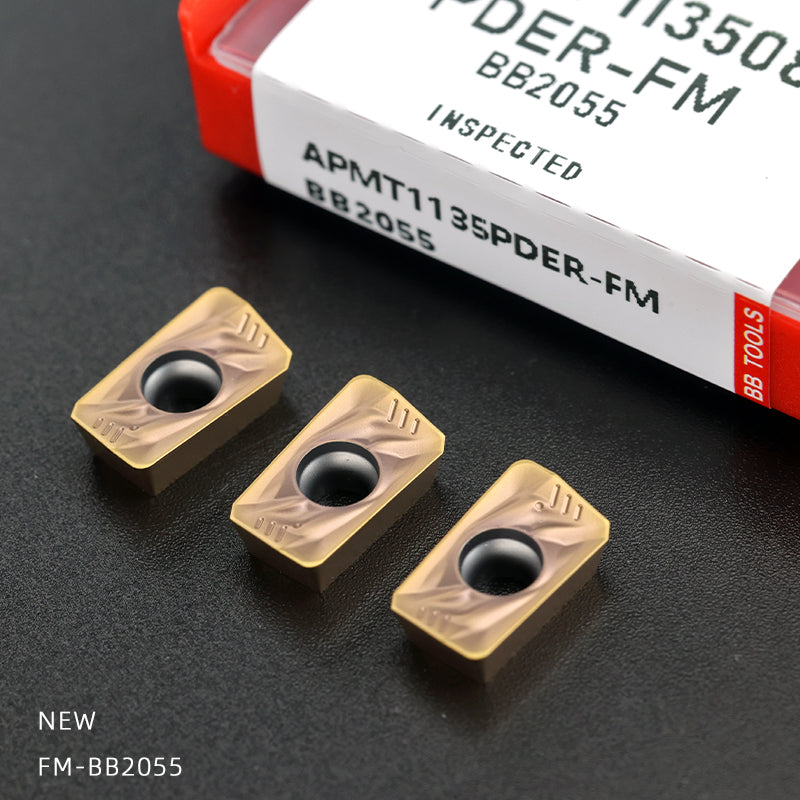
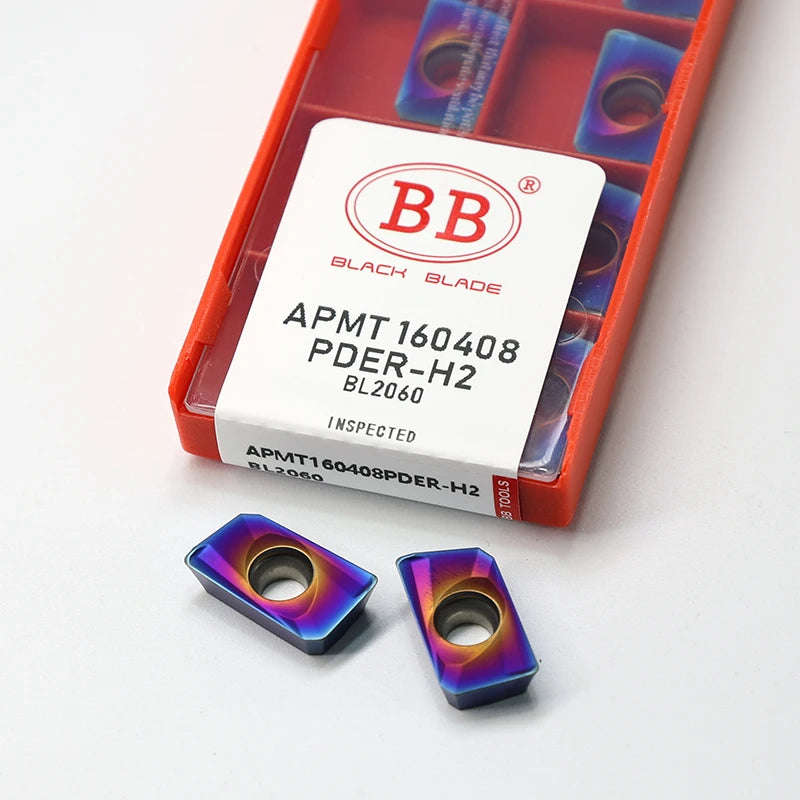
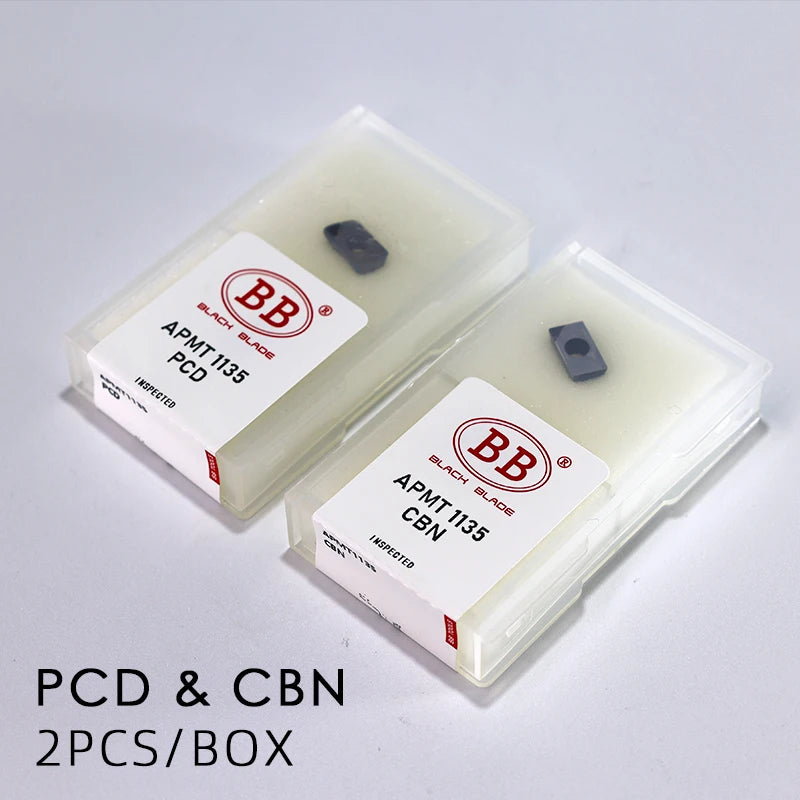
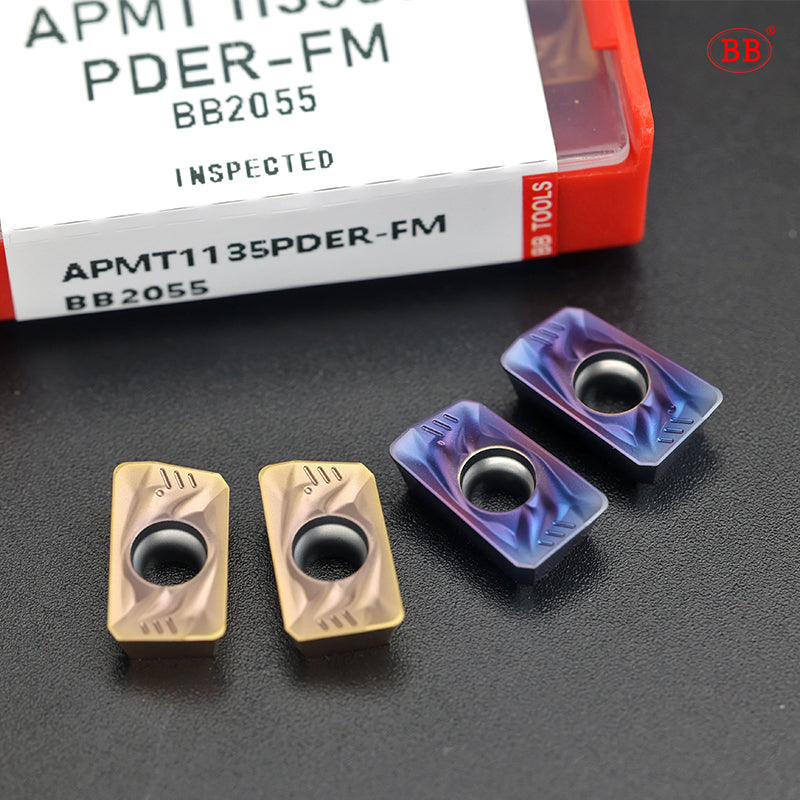
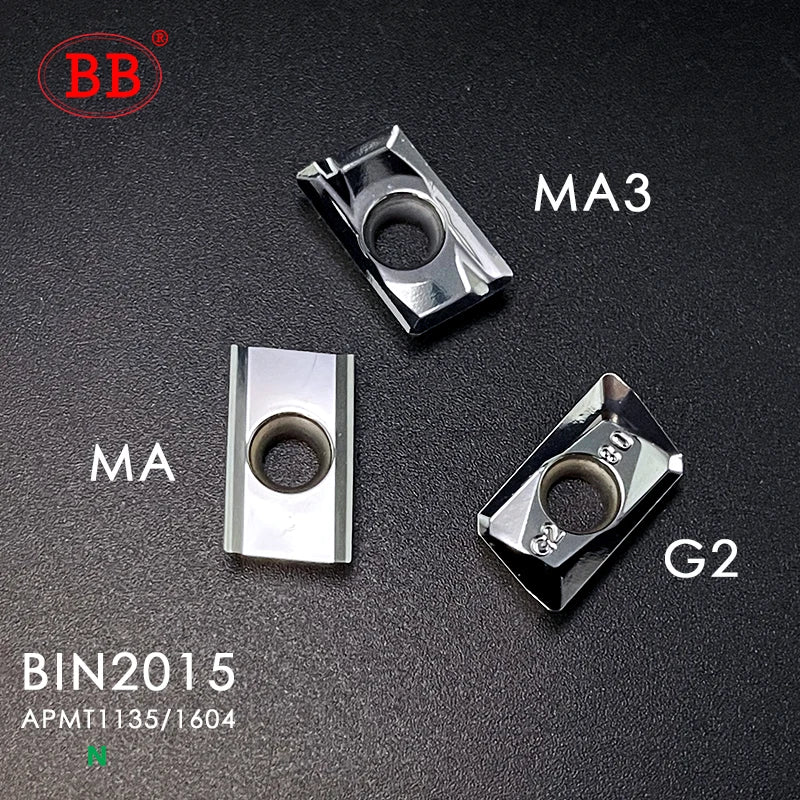

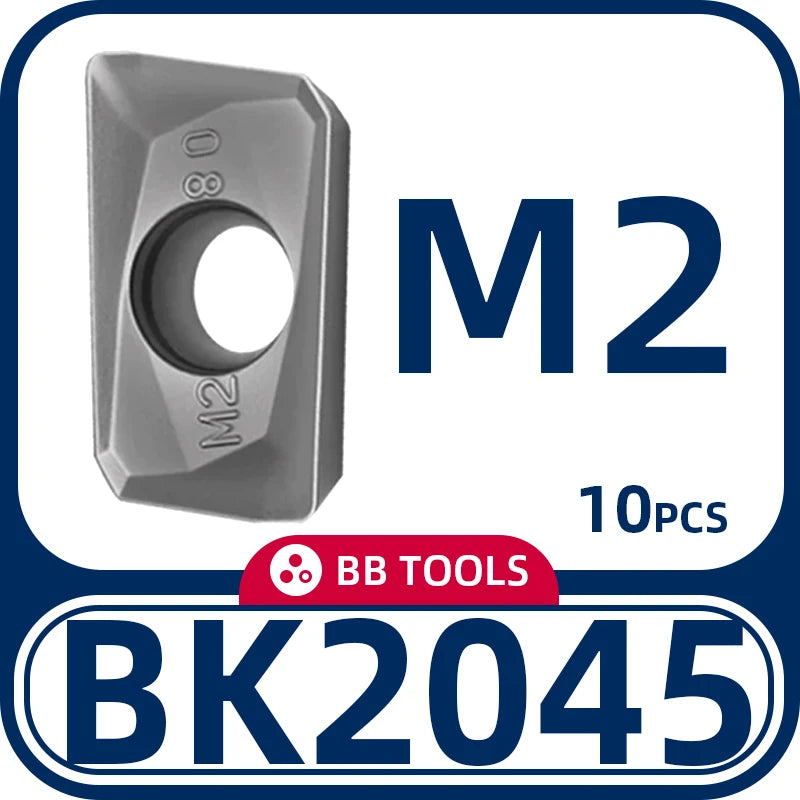
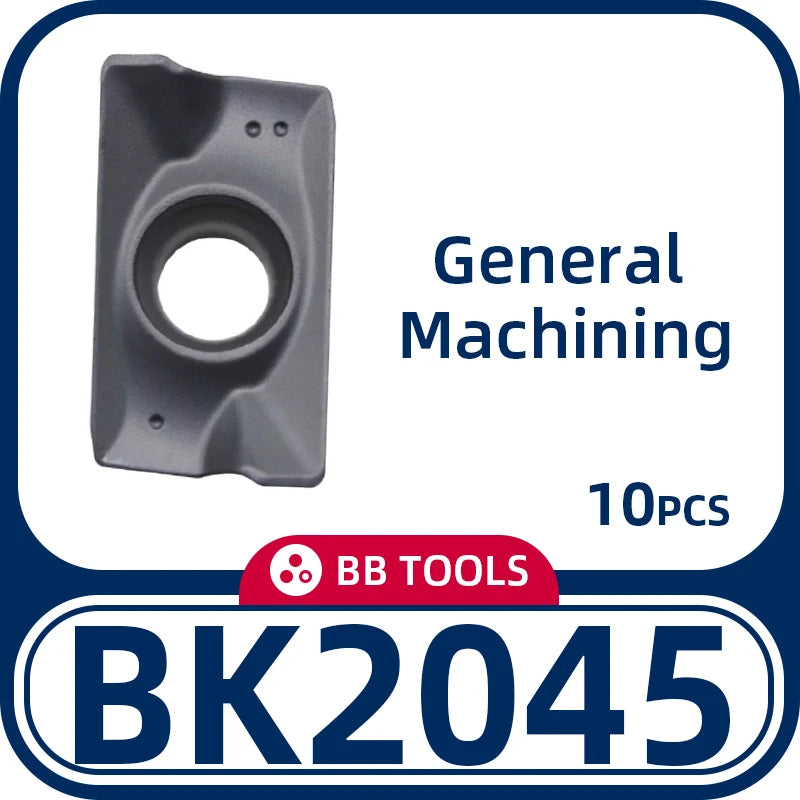
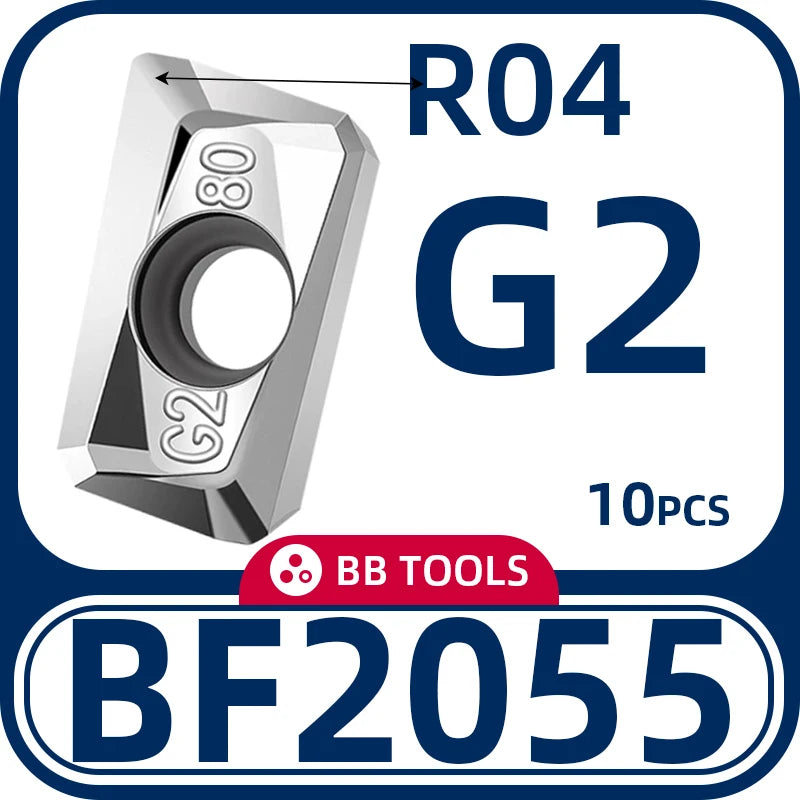
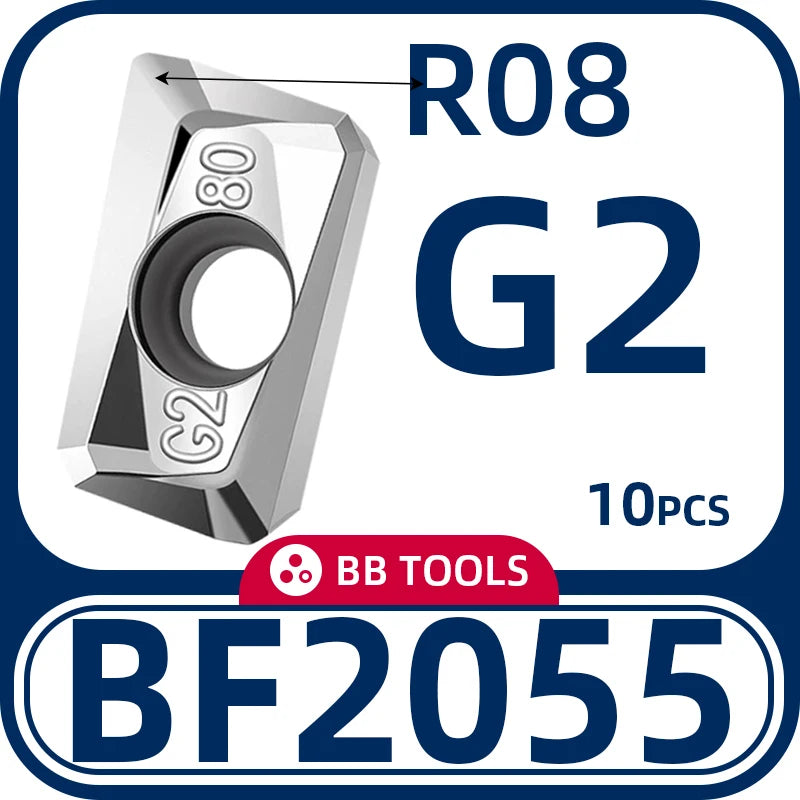
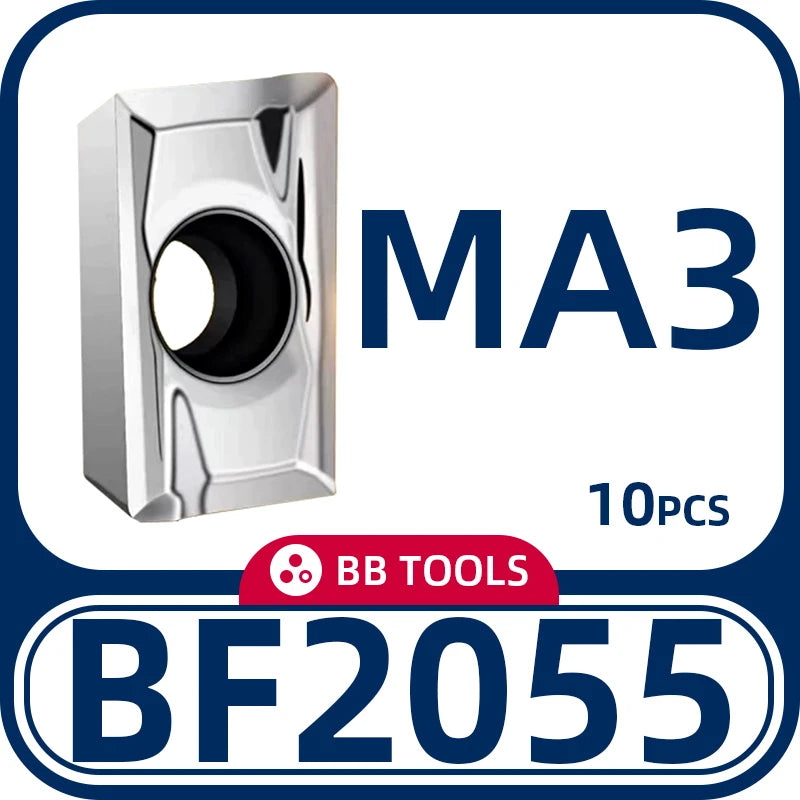
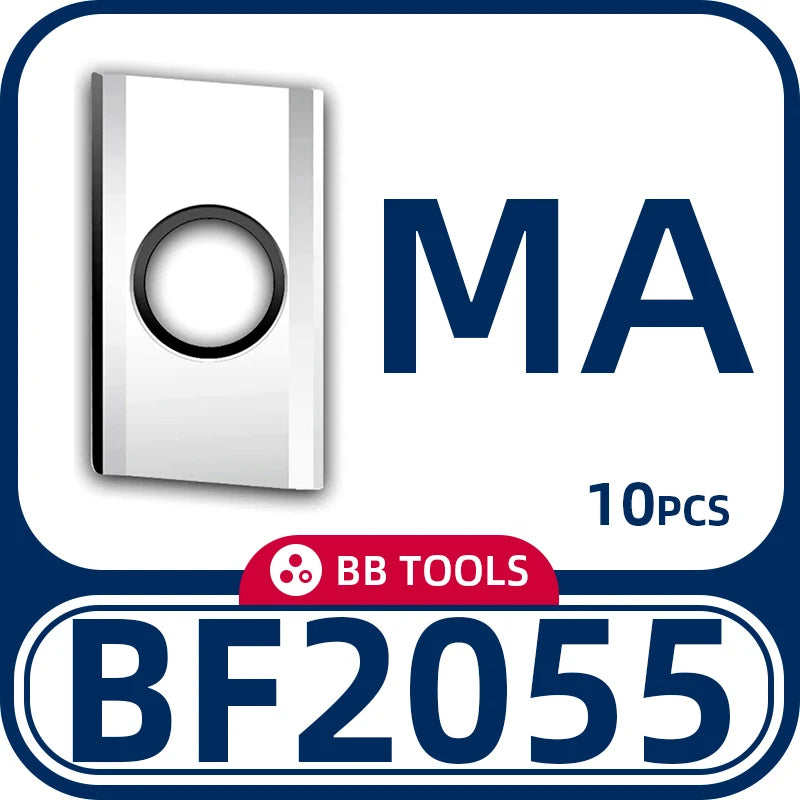
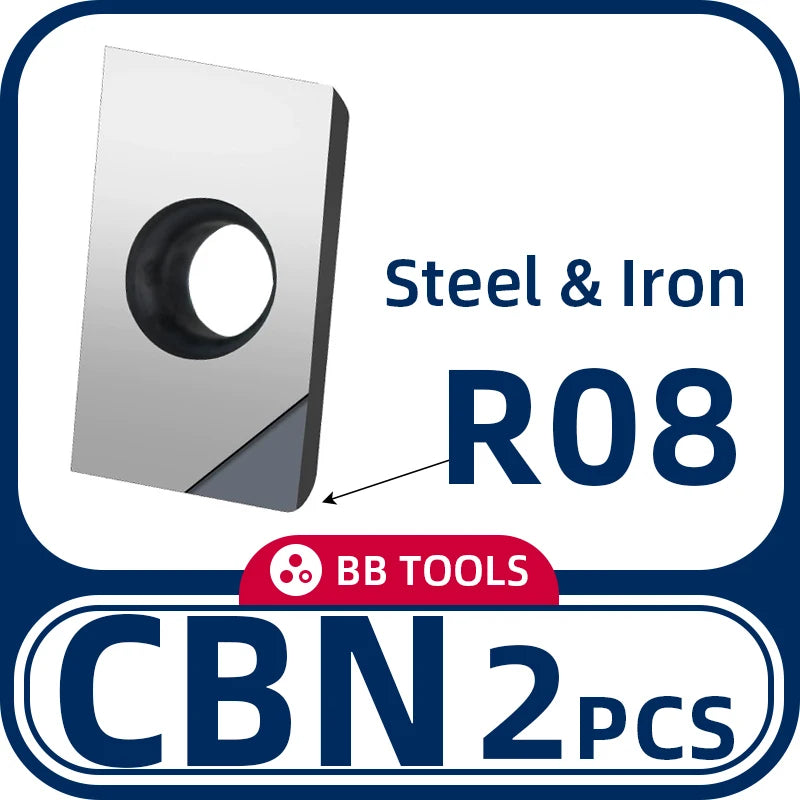
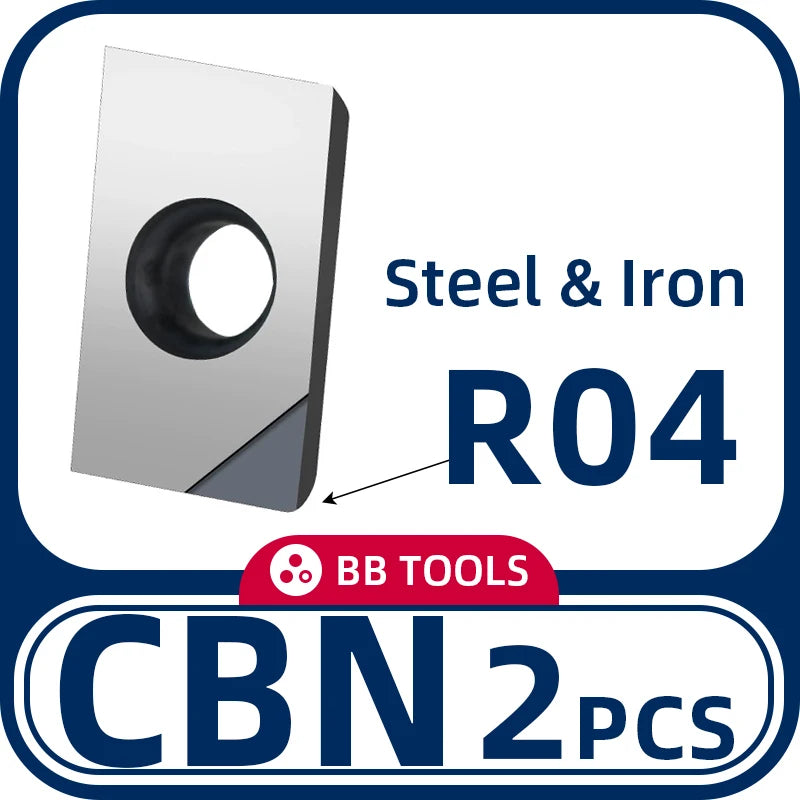
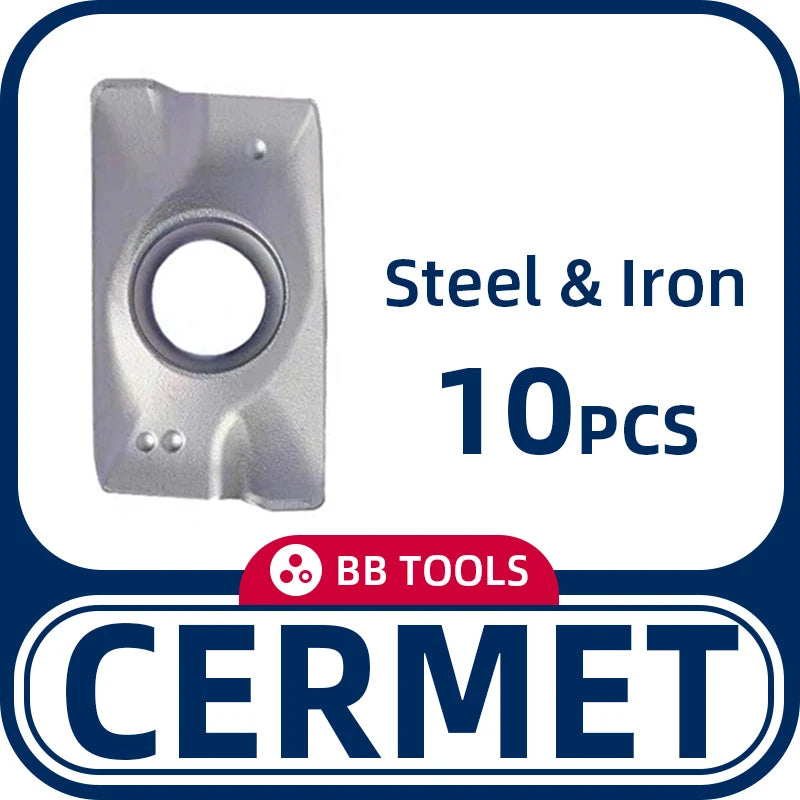
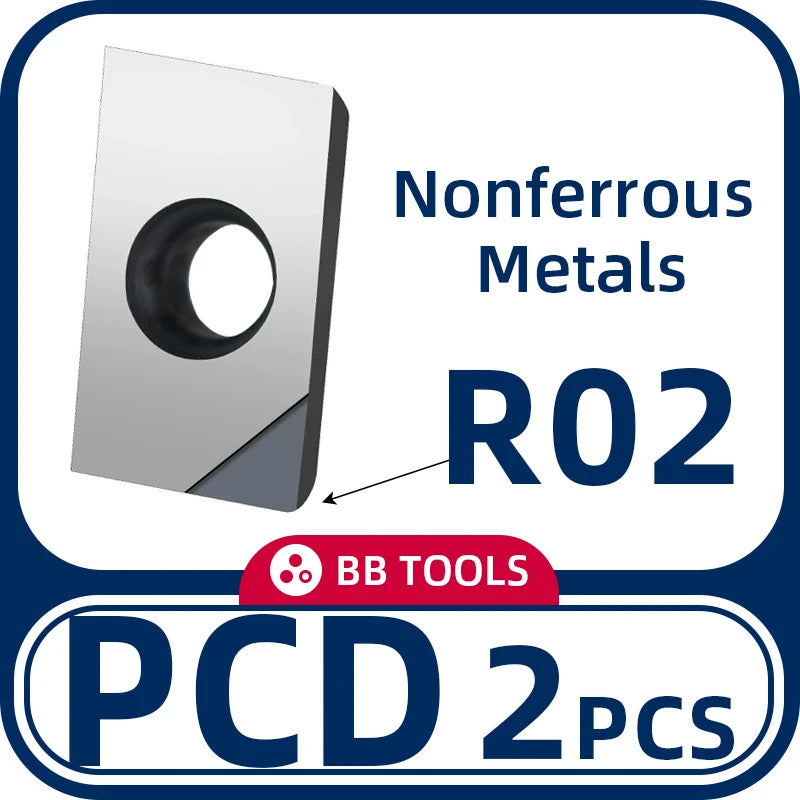
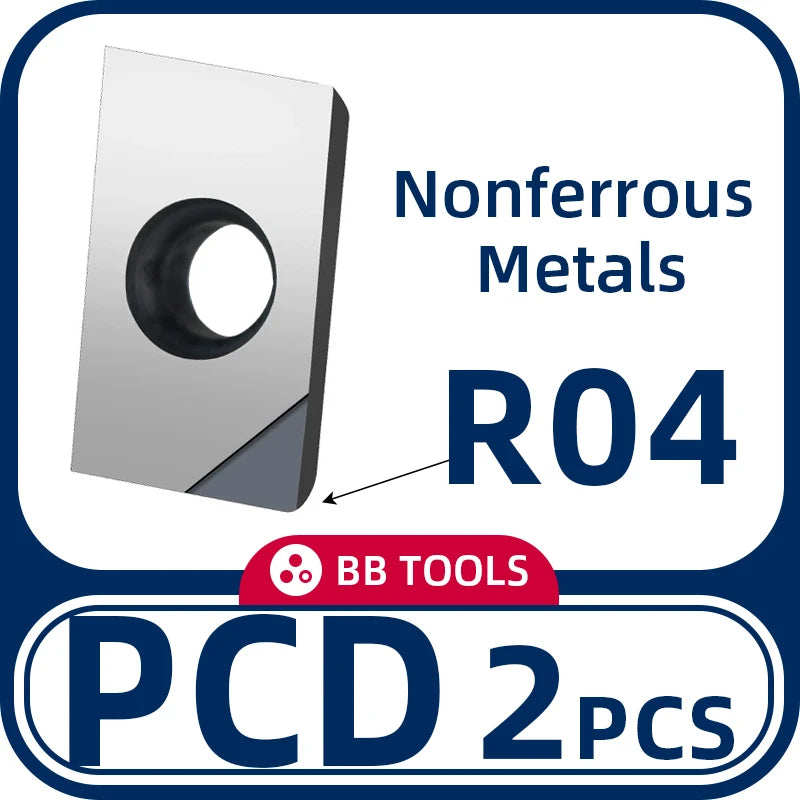
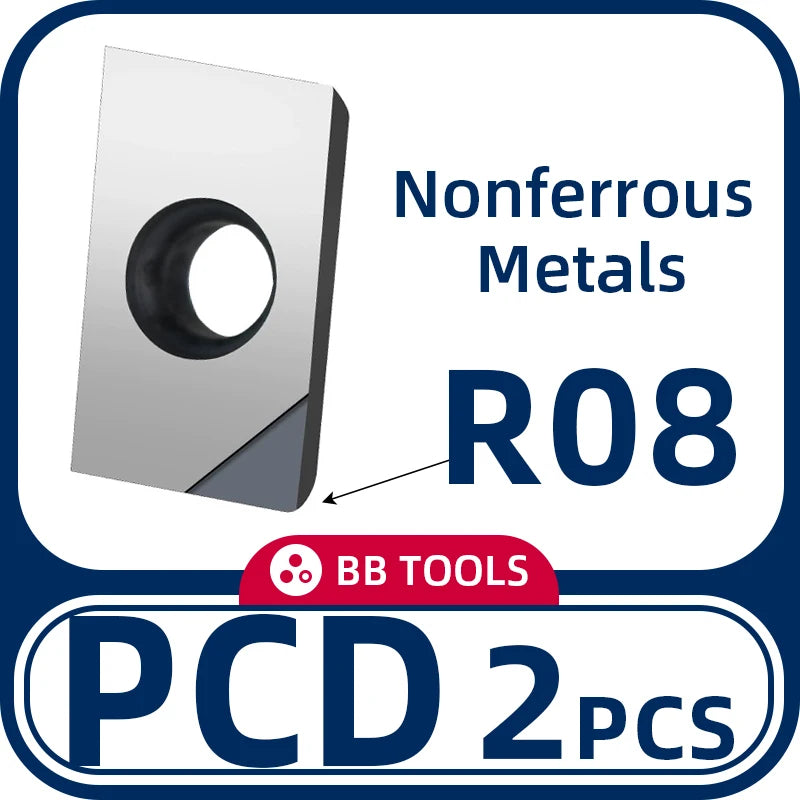
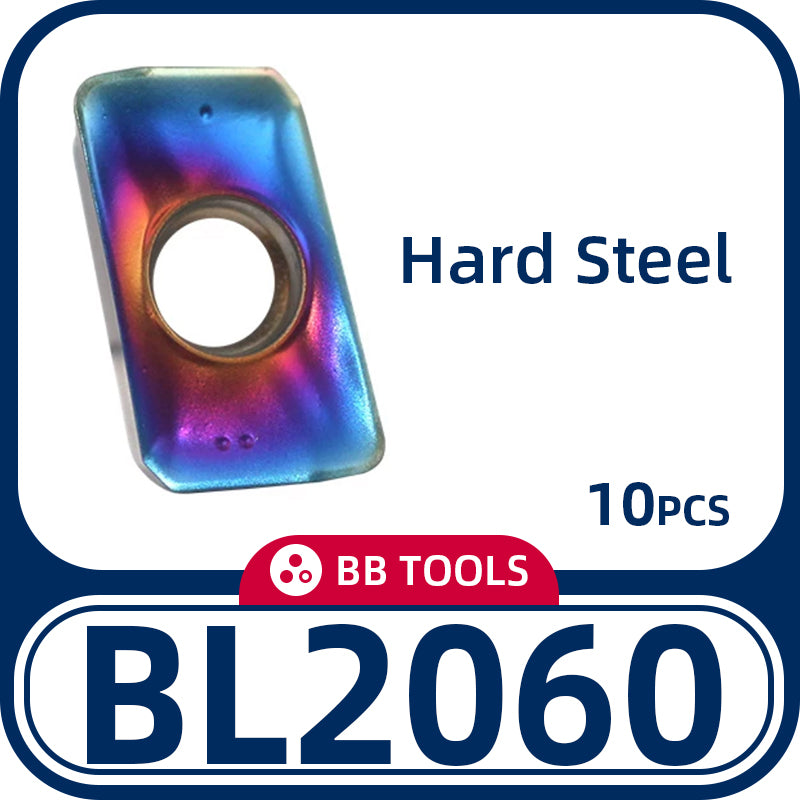
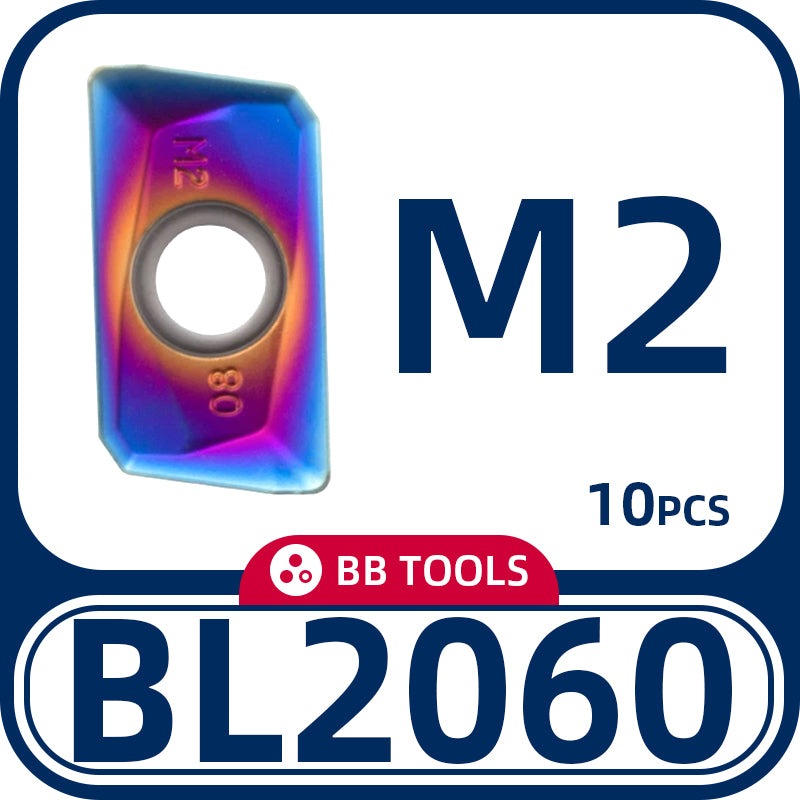
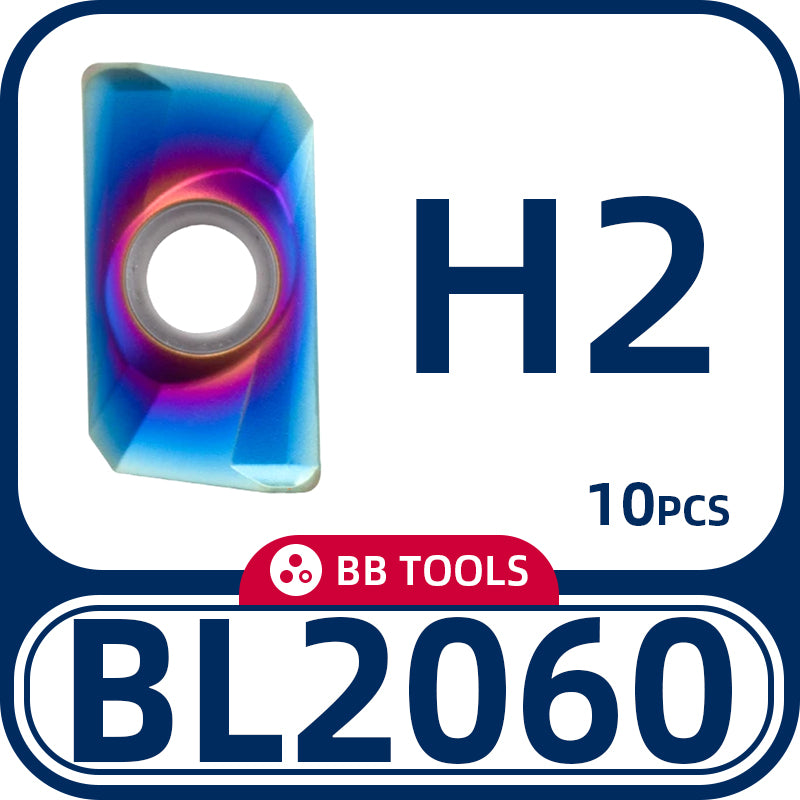
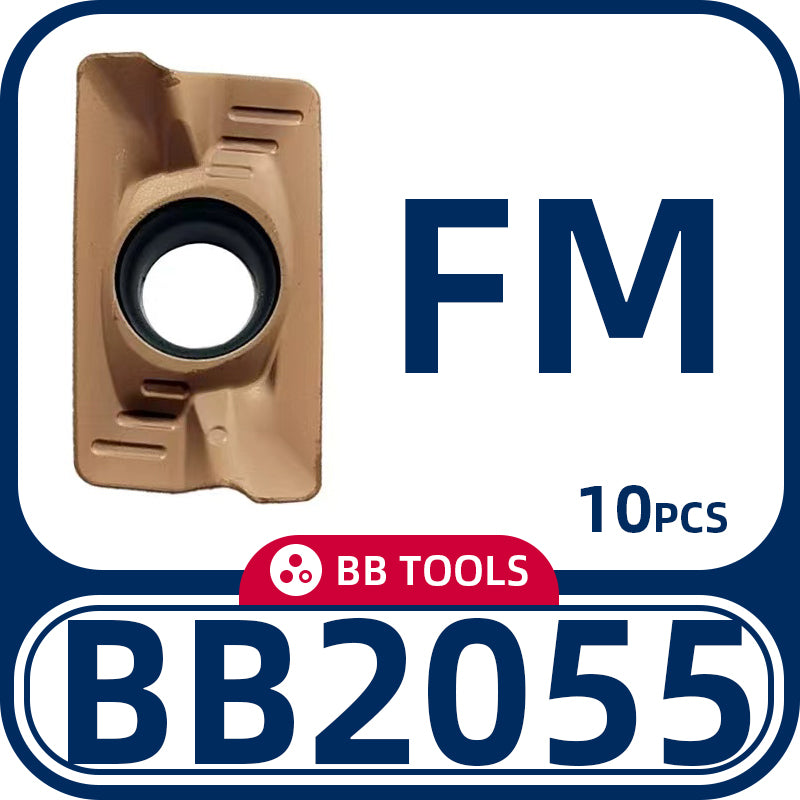